Wire Wrapped Pre Packed Sand Control Oil Well Screens
Pre packed Sand Control Oil Well Screens contains perforated base pipe, inner and outer screen jackets and graded sand between the jackets. It is a modification of wire wrapped screen which is used in well sorted sand or stand-alone completion. Graded sand, with or without resin coating, is considered as a filter for reservoir particles.
Wire wrapped pre packed sand control screen is used in wells where conventional gravel packing is not feasible or economical. The thickness of gravel layer can be varied to meet special requirement.
What Is the Function of Gravel Pack?
Gravel packing is one of popular sand-control technique used in oil, water and gas wells. It stabilizes the borehole and filters the sand from the flow, only allowing very fine particles in. Pre packed wire wrapped sand screen brings it into full play in maximizing production as well as controlling the sand.
Custom Service
Pre packed wire wrapped sand control screen can be customized to catch up with your special requirement. Gravel sizes, sand coating and pack thickness are changeable according to your need. Material grades for the screen and pipe are manufactured according to API tubing or casing from stainless steel 304, 316L, 904, Alloy 825/625/C276. End fittings and threaded connections are bespoke too.
Feature & Advantages:
- Outer V shaped screen is more flexible and provides more area;
- Pre pack screen filters out formation sand;
- Close contact with aquifer enhancing well performance;
- Economical alternative to cased-hole gravel packs;
- Smaller borehole;
- Custom design available.
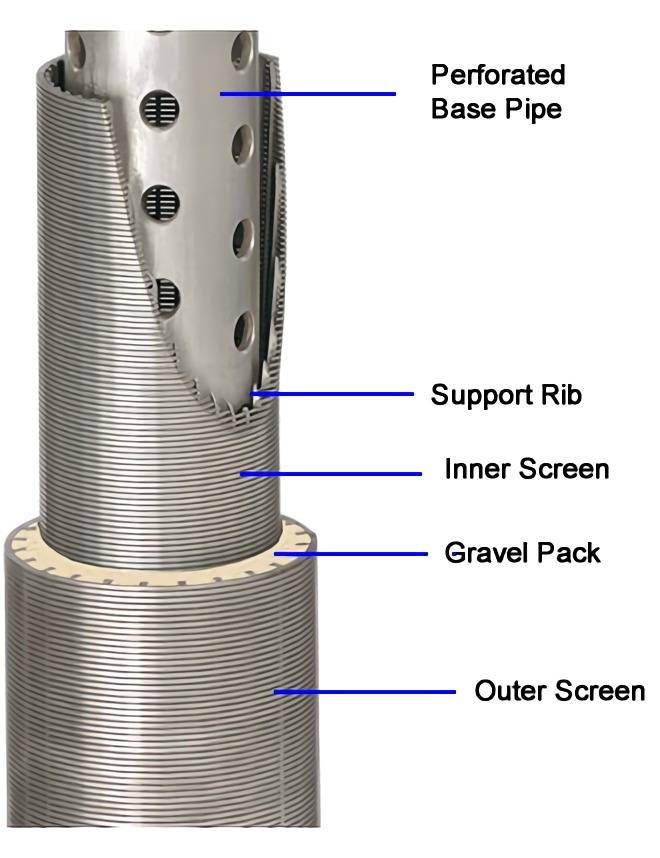
Pre Packed Sand Screen
Casing Size (in) | Outer Screen OD (in.) | Inner Screen OD (in.) | Basepipe OD (in.) | Basepipe ID (in.) | Coupling OD (in.) |
---|---|---|---|---|---|
4 1/2 | 2.55 | 1.45 | 1.05 | 0.824 | 1.313 |
5 | 3.48 | 2.365 | 1.900 | 1.610 | 2.200 |
5 1/2 | 4.13 | 2.856 | 2.375 | 1.995 | 2.875 |
6 5/8 | 4.64 | 3.365 | 2.875 | 2.441 | 3.500 |
7 | 5.12 | 3.965 | 3.500 | 2.992 | 4.250 |
7 5/8 | 5.64 | 3.965 | 3.500 | 2.992 | 4.250 |
7 5/8 | 5.64 | 4.490 | 4.000 | 3.548 | 4.500 |
7 5/8 | 6.19 | 4.980 | 4.500 | 4.000 | 5.000 |
8 5/8 | 7.23 | 5.475 | 5.000 | 4.408 | 5.563 |
9 5/8 | 8.23 | 5.980 | 5.500 | 4.950 | 6.050 |
9 5/8 | 8.23 | 7.10 | 6.625 | 6.065 | 7.390 |
Slotted Liner – API Base Pipe Sand Control Oil Well Screens
Slotted liner or standalone screen is a popular sand control screen in long horizontal completions and low productivity wells. Precision slotted liners are manufactured by CNC controlled slotting machines or laser machine. All slots are de-burred, cleaned and drift tested according to API standards. Base pipe are per API casing or tubing specification with diameters from 1.5 inch to 18 inch. Pipe lengths of any diameter are available.
Slot Size
Slot size including slot width and length is customized to suit customer’s requirement. For straight or keystone slots, minimum slot width is 0.012 inch and maximum slot width would be 0.25 inch.
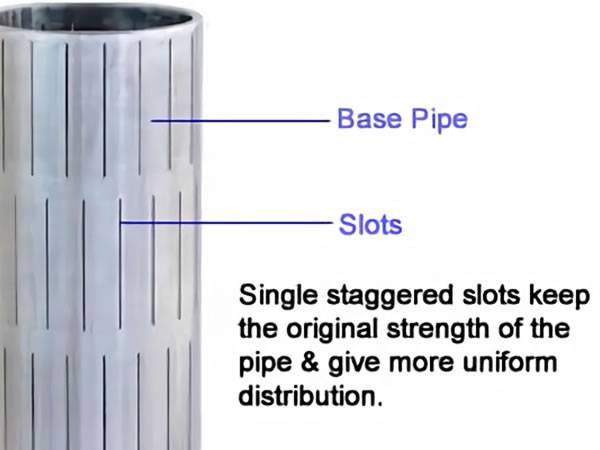
Slot Liner
1.5 inch long | 2.0 to 2.5 inch long | 2.5 inch long |
---|---|---|
0.012 inch wide | 0.024 inch wide | 0.078 inch wide |
0.015 inch wide | 0.025 inch wide | 0.125 inch wide |
0.016 inch wide | 0.038 inch wide | 0.250 inch wide |
0.018 inch wide | 0.048 inch wide | – |
– | 0.058 inch wide | – |
Slotting Pattern
- A: refers to single staggered slots.
- B: refers to straight slots.
- C: refers to multiple staggered slots.
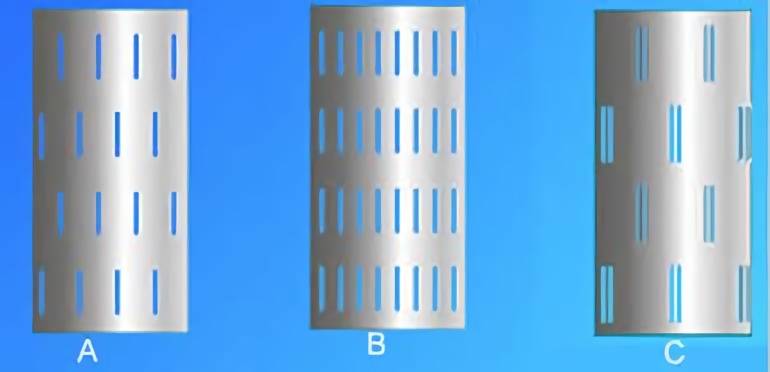
Slot Pattern
Slot Shape
Straight Slot
Straight slot has straight sides with equal width through the wall of the casing. It is normally used in consolidated formations or when slots of 0.030” or wider are specified.
Pros: Higher resistance to wear and more economical than keystone.
Cons: The possibility of clogging is higher than keystone slot.
Keystone slot is like a reversed “V” with narrower spacing at the liner surface and wider spacing in the inside casing wall. This shape allows for sand grains to bridge across the opening and ensures all the particles that enter into the hole will completely go through the wall.
Pros: Keystone shaped slots substantially reduce the possibility of clogging and improve work efficiency.
Cons: A little expensive than straight slotted liner.

Slot shape
Applications:
Slotted liners are suitable for gravel packed completions or stand-alone completion where grain size is large.
How Many Holes Needed To Achieve a Certain Open Area?
- N =
- N = the number of slots per foot.
- D = Outside diameter of the liner (in inches).
- C = Open area percentage.
- W = selected slot width (in inches).
- L = Length of slot (inches).
Manufacturing process of Sand Control Oil Well Screens.
Table of Contents
Introduction 3
History of Oil Well Screens 3
Types of Oil Well Screens 4
Raw Materials 5
Design Considerations 6
Manufacturing Process 7
Step 1: Design 7
Step 2: Cutting and Shaping 8
Step 3: Bending and Welding 8
Step 4: Finishing 9
Step 5: Testing and Quality Assurance 9
Conclusion 10
References 11
Introduction
Oil well screens are an essential component of the oil and gas industry. They are used in the production of oil and gas from a well, providing a barrier between the reservoir and the wellbore to allow oil and gas to flow through, while preventing sand, sediment, and other debris from entering the well. The size, shape, and material of the oil well screens are all important factors in ensuring that the screens are able to perform their intended function.
Due to their importance in the oil and gas industry, the manufacturing of oil well screens requires a high level of precision and accuracy. There are several steps involved in the manufacturing process, from the initial design to the final testing and quality assurance. This article will discuss the different stages of the oil well screen manufacturing process and the considerations that go into each step.
History of Oil Well Screens
The history of oil well screens dates back to the late 19th century, when the first oil wells were drilled in the United States. Early oil wells used a variety of different materials to create screens, such as metal mesh and wooden frames. However, these early screens were not very effective and often failed to prevent sand and other debris from entering the wellbore.
The first successful oil well screen was developed in the 1920s. This screen was made of metal mesh and was designed to be strong enough to prevent sand and other debris from entering the wellbore, while still allowing oil and gas to flow through. This design was used for many years, until the development of more advanced materials and designs made it possible to create more efficient and effective oil well screens.
Types of Oil Well Screens
There are several different types of oil well screens available, each with its own unique set of characteristics. The most common types of oil well screens are wire-wrapped screens, slotted liner screens, perforated pipe screens, and expandable screens.
Wire-wrapped screens are made from a continuous length of wire that is wound around a series of metal rods. These screens are strong and durable, and they are able to effectively prevent sand and other debris from entering the wellbore.
Slotted liner screens are made from a continuous length of metal with a series of slots cut into it. This design allows oil and gas to flow through the slots, while preventing sand and other debris from entering the wellbore.
Perforated pipe screens are made from a continuous length of metal pipe with a series of holes drilled into it. This design allows oil and gas to flow through the holes, while preventing sand and other debris from entering the wellbore.
Expandable screens are made from a flexible material that can be expanded to fit the size and shape of the wellbore. This design allows for a more uniform flow of oil and gas, while still preventing sand and other debris from entering the wellbore.
Raw Materials
The raw materials used in the manufacturing of Sand Control Oil Well Screens vary depending on the type of screen being produced. Wire-wrapped screens are typically made from stainless steel, mild steel, or brass wire, while slotted liner screens are typically made from stainless steel, mild steel, aluminum, or copper. Perforated pipe screens are typically made from stainless steel, mild steel, or aluminum, while expandable screens are typically made from stainless steel, mild steel, aluminum, or brass.
Design Considerations
The design of an Sand Control Sand Control Oil Well Screens is a crucial factor in its effectiveness and efficiency. The design must be tailored to the specific application and must take into account factors such as the size and shape of the wellbore, the type of oil and gas being produced, and the type of sand and other debris that may be present.
The design must also be able to withstand the pressure and temperature of the oil and gas being produced, as well as the corrosive nature of the environment. The design must also be able to handle the flow of oil and gas while preventing sand and other debris from entering the wellbore.
Manufacturing Process
The manufacturing of oil well screens involves several steps, from the initial design to the final testing and quality assurance.
Step 1: Design
The first step in the manufacturing process is the design of the screen. The design must be tailored to the specific application and must take into account factors such as the size and shape of the wellbore, the type of oil and gas being produced, and the type of sand and other debris that may be present.
The design must also be able to withstand the pressure and temperature of the oil and gas being produced, as well as the corrosive nature of the environment. The design must also be able to handle the flow of oil and gas while preventing sand and other debris from entering the wellbore.
Step 2: Cutting and Shaping
Once the design has been completed, the raw materials are cut and shaped to the desired specifications. This step involves cutting the raw materials to the desired size and shape, as well as drilling any holes that may be needed.
Step 3: Bending and Welding
Once the raw materials have been cut and shaped, they are bent and welded together to create the desired shape and size of the screen. This step involves welding the components of the screen together, as well as bending the components to the desired shape and size.
Step 4: Finishing
Once the screen has been welded and bent, it is then finished. This step involves treating the screen to prevent corrosion, as well as adding any additional features that may be needed.
Step 5: Testing and Quality Assurance
Once the screen has been finished, it is then tested to ensure that it meets the desired specifications and performance requirements. This step involves testing the screen for strength, durability, and efficiency.
Conclusion
Oil well screens are an essential component of the oil and gas industry, providing a barrier between the reservoir and the wellbore to allow oil and gas to flow through, while preventing sand, sediment, and other debris from entering the well. The manufacturing of oil well screens is a complex process, involving several steps from the initial design to the final testing and quality assurance. This article has discussed the different stages of the oil well screen manufacturing process and the considerations that go into each step.
References
Boswell, S., & Smith, J. (2012). Oil and Gas Wells: Types of Well Screens. Retrieved from https://www.oil-and-gas-wells.com/types-of-well-screens/
Hassan, S., & Bhat, S. (2020). Design and Manufacturing of Oil Well Screens. Retrieved from https://www.intechopen.com/books/oil-and-gas-industry/design-and-manufacturing-of-oil-well-screens
Stuart, N. (2020). How Are Oil Well Screens Manufactured? Retrieved from https://www.wisegeek.com/how-are-oil-well-screens-manufactured.htm