Mill Sloted well screen
Another vertically slotted screen is manufactured from casing by milling openings with axially oriented cutters. This product is
designed for use in oil wells where fluid production is very low. Its disadvantages include clogging due to the parallel surfaces
within the opening. Since slot clogging is directly related to wall thickness, thicker material encourages greater plugging. Some vertical mill slotted casings are machined with an undercut to reduce this tendency. A second drawback is low area of opening, although this can be overcome at higher cost by increasing the number of slots. Collapsing strength of vertically slotted casings, however, is substantially reduced when the number of openings is increased
Field experience has proved that development is generally slower in wells screened with milled slot casings. Another aspect of vertical slots compared with horizontal openings is that sand and gravel control is less positive. A smaller aperture and/or larger grav Meanwhile, the laser incision can make very small cuts with smooth surface and high precision. Although its structure is simple, it is very effective. It has small cuts of 0.1-0.5mm in the tube wall.
API Casing | ID mm | Length m | Slot Length mm | Slot No.No./m | Slot width mm | Slot Tolerance | Valid Filter Area cm/m | Max. Strength KN | ||
Spec mm | Thickness mm | Per Weight kg/m | ||||||||
60.32 | 5 | 6.84 | 50.3 | 3 | 80 | 200 | 0.3 | ±50 | 48 | 512.54 |
73.02 | 5.5 | 9.15 | 62 | 240 | 57.6 | 688.55 | ||||
88.9 | 6.5 | 13.22 | 75.9 | 280 | 67.2 | 995.1 | ||||
101.6 | 6.5 | 15.22 | 88.6 | 300 | 72 | 1151.2 | ||||
114.3 | 7 | 18.47 | 100.3 | 10 | 320 | 76.8 | 1400.4 | |||
127 | 7.52 | 22.13 | 112 | 340 | 81.6 | 1673.8 | ||||
139.7 | 7.72 | 25.11 | 124.3 | 360 | 86.4 | 1900.2 | ||||
9.17 | 29.48 | 121.4 | 360 | 86.4 | 2232.4 | |||||
168.3 | 8.94 | 35.09 | 150.4 | 400 | 96 | 2672.95 | ||||
177.8 | 8.05 | 33.68 | 161.7 | 440 | 105.6 | 2559.2 | ||||
9.19 | 38.19 | 159.4 | 440 | 105.6 | 2940.7 |
Wrap Screen & Bridge Slot well screen
Wire Wrap well screen
One well-known well screen is manufactured by wrapping a wire around longitudinal rods. The wire is welded to the rods by resistance welding producing a cage-shaped cylindrical configuration. This type of screen, commonly known as wire-wrap or continuous slot, is usually manufactured from type 304 stainless steel, galvanized steel and carbon steel.
The continuous slot design originated in the early part of this century to overcome the problems of ground-water development from distinctive aquifers associated with the North Central United States. These aquifers were generated from rock picked up, broken, and pulverized by advancing glaciers during the Ice Ages. While glacial till is not well sorted, occasionally thin layers of finegrained, uniform sands were washed from the original deposits. Such materials are high yielding water producing formations. Prior to the advent of rotary well construction and the gravel envelope well design, it was difficult to produce the full capacity of sand free water from these aquifers.
Material
|
SS304, SS304L, SS316, SS316L, SS321, Duplex, Hastelloy, etc
|
|||
External diameter
|
25–300mm
|
|||
Standard
|
Non-standard, OEM, ODM
|
|||
Specification
|
Easy leakage, wear resistance, corrosion resistance. The mesh cross section is a trapezoid, narrow width of the gap, have a wire
made of cold rolled stainless steel, this wire is support rods. The screen is uniform, the welding is stable, high hole rate, long service life, high strength, stiffness and bearing capacity of rigid, screening filter device can be made into various shapes. |
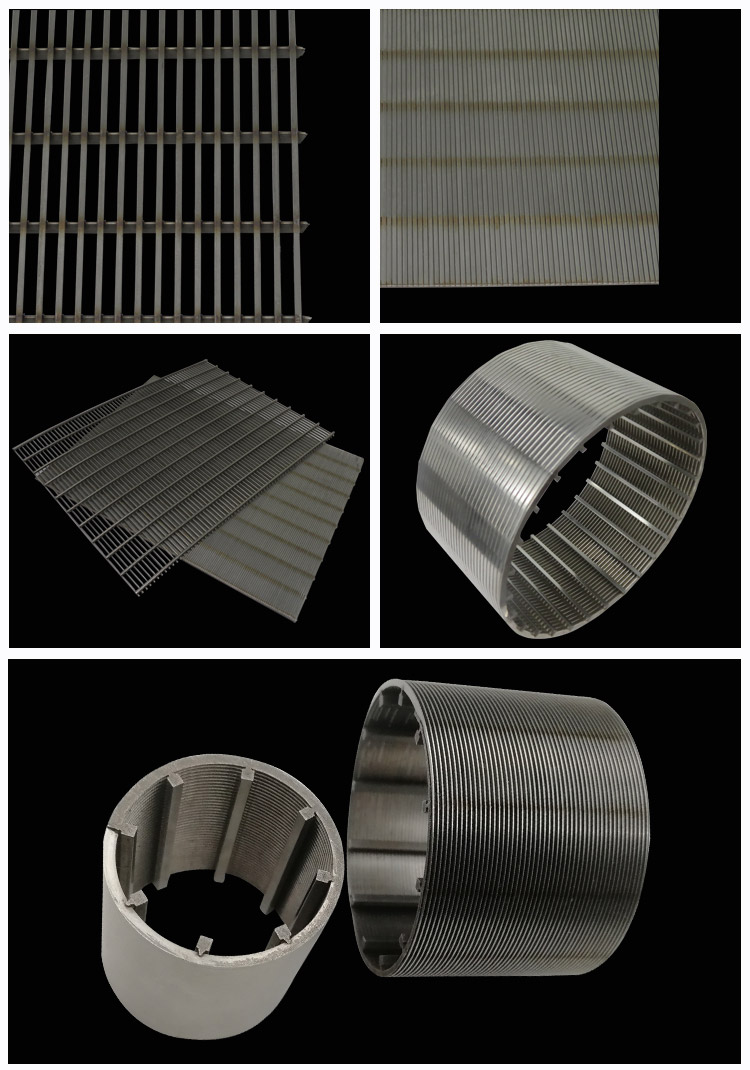
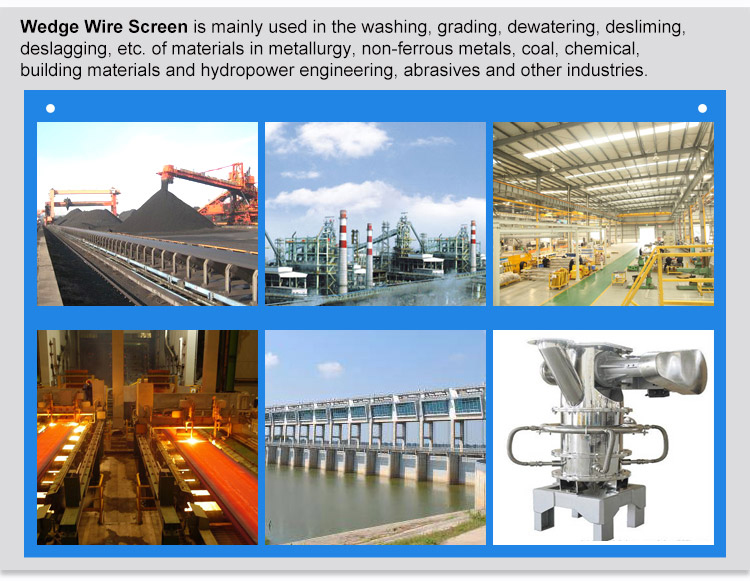
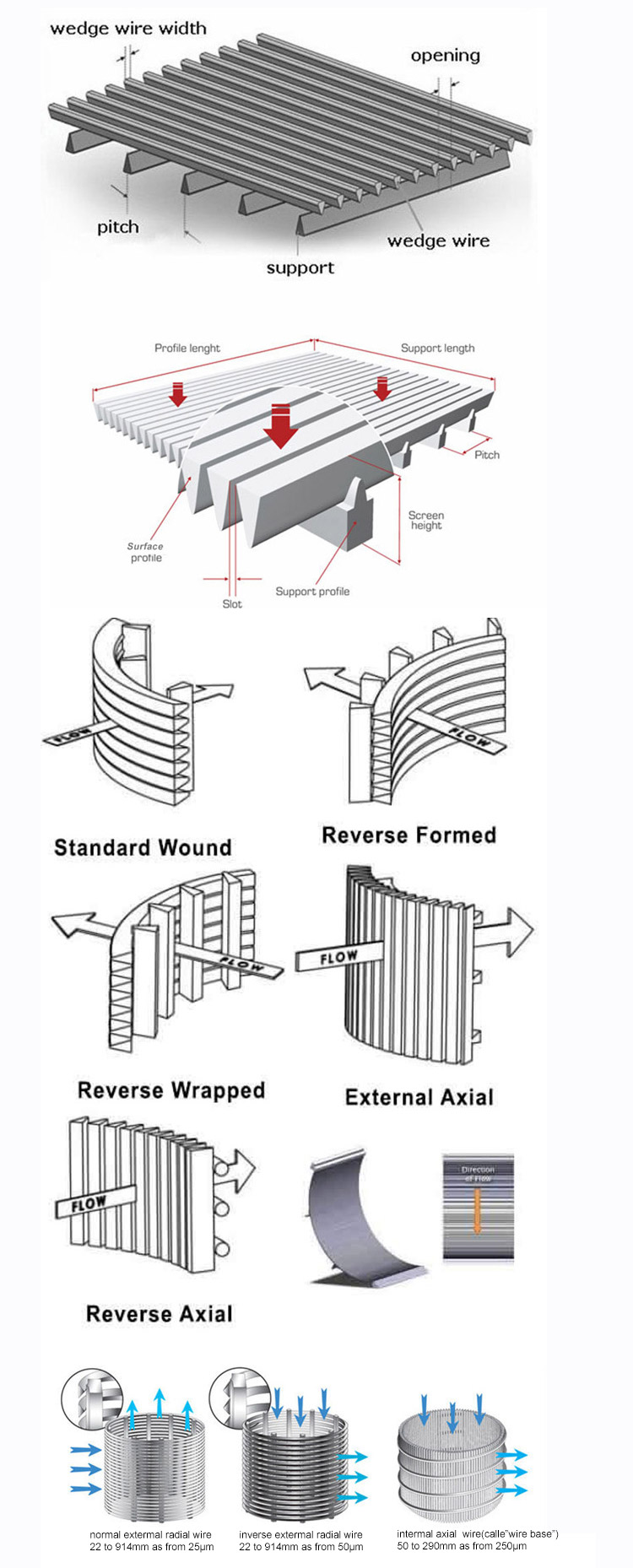
A well design incorporating wire-wrap screen was developed to meet these conditions, and proved successful. The characteristics of wire-wrap screen are well suited for its original purpose. This design offers the highest surface area of opening of any screen. Consequently, with very small aperture sized (.005 in. to .035 in.) necessary to control fine sands from thin aquifers without a gravel envelope, sufficient area of opening is still available to minimize frictional head losses through the screen. However, under such circumstances, stainless steel must be used since enlargement of openings result in sand pumping.
The manufacturing process lends itself to close tolerances required for very fine aperture sized and the V-shaped slot configuration reduces clogging. Careful consideration must be made of the use of wire-wrap screen in situations or under conditions for which it was not originally designed. It is generally more costly than other types without necessarily providing higher production, better efficiency or greater durability. Screen of this design, including most higher cost, heavy duty versions with bigger rods, wire or both, has lower collapsing strength than other screen types and usually lower than the well casing it is installed with. Special care should be taken in installation. The configuration of wire-wrap screen makes it difficult to swab, a simple and very effective method of well development, redevelopment and cleaning. This is because the internal surface of the screen is not a smooth circle due to the cross sections of the vertical rods. Close fitting swabs cannot be employed effectively because water bypasses through the annulus between the rods instead of surging in and out of the formation and filter pack. Development with air or high velocity jetting is not as effective a development method, especially in gravel envelope wells.
For similar reasons cleaning and removal of encrustations is more difficult, requiring acidizing rather than removal by mechanical methods. Wire-wrap screens are also more difficult or impossible to repair or restore to their original shape and structural integrity. Extra caution must be exercised using down-the-hole tools. Finally, the high area of opening, which may be an asset under certain conditions, acts adversely in the carbon steel version. The surface area exposed to corrosion is in the order of three times that of other types of screens. This results in faster loss of weight and strength.
Since wire-wrap screen was originally developed for use in non-gravel envelope wells, its use in gravel envelope wells must take into consideration the requirements of that design for success. Avoid the practice of selective screening for reasons mentioned earlier. Do not use too small a screen aperture size. With a properly designed gravel envelope well there is seldom any condition requiring an aperture size less than .040 inches. However, in this regard, it is important to note that while the V-shaped orifice of continuous slot screen reduces clogging it does not encourage stabilization of the gravel envelope particles. The recommended aperture size is that which will retain 90% of the filter pack. This results in a smaller aperture size than is possible with some other screen designs. A less expensive wire-wrap screen fabricated from round galvanized steel wire is available. This wire shape encourages plugging through the forming of particles in the narrow orifice.
Bridge Slot well screen
Another well screen produced in the United States and overseas is referred to as “bridge slot”. This screen is manufactured on a press from flat sheets or plates. The slot opening is usually vertical and provides two orifices, longitudinally aligned to the axis.
The perforated steel sheets or plates are then rolled into cylinders and the seam welded. Normally five foot sections of bridge slot screen are welded together into longer lengths suitable for field installation.
Bridge slotted screen is normally used in water wells for sand controlling. It is manufactured from precision punched quality metal sheet including ST37-2 or stainless steel 304/316L. The slots are punched in a flat sheet and at the same time the sheet is rolled into a tube and welded. Slots are arranged in staggered arrangement to reduce negative effect on the screen’s strength.
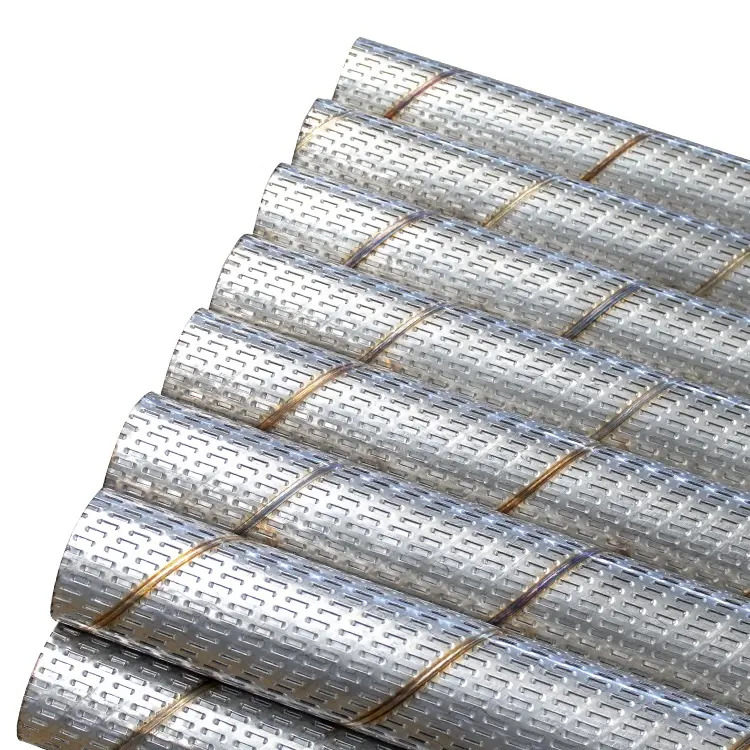
Bridge sand control screen
Product Description:
- Wall thickness: 3.5 mm to 7 mm;
- Open area: up to 12%;
- Slot width: 1 mm to 4 mm;
- Outside diameter: 6 5/8”, 7”, 8”, 9 5/8”, 10 3/4” & 12”.
Feature & Advantage:
- High mechanical strength;
- Economical price;
- Easy installation;
- Precision slot opening;
- Large open area.
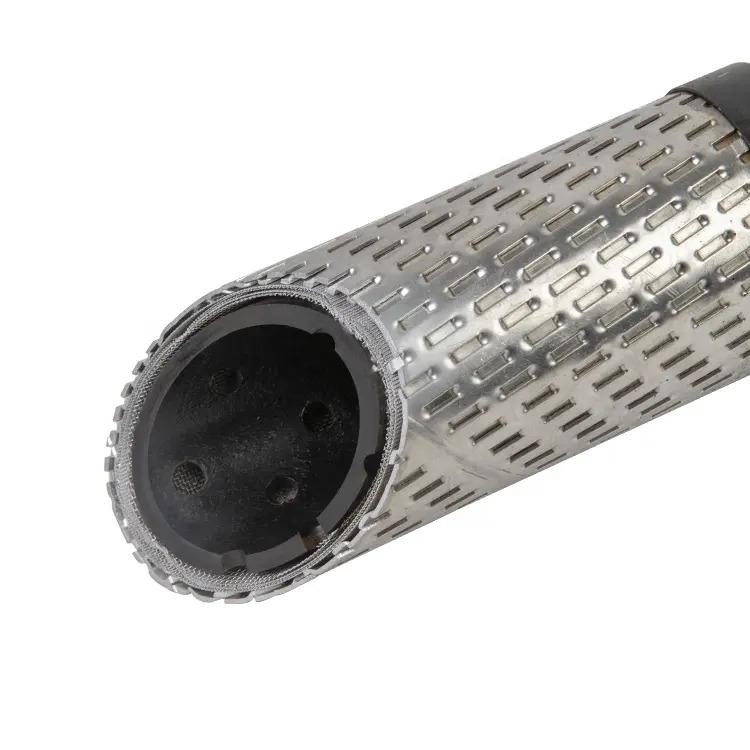
Bridge slot screen is usually installed in gravel envelope wells. Its chief advantages are reasonably high area of opening and inimum frictional head losses ate relatively low cost. One important disadvantage is low collapsing strength due to the large number of vertically oriented slots. The manufacturing process is limited with respect to wall thickness and .250 inch is the maximum generally available. Since gravel control is more difficult with any vertical opening as compared to a horizontal opening, a smaller aperture size relative to the pack material should be selected.